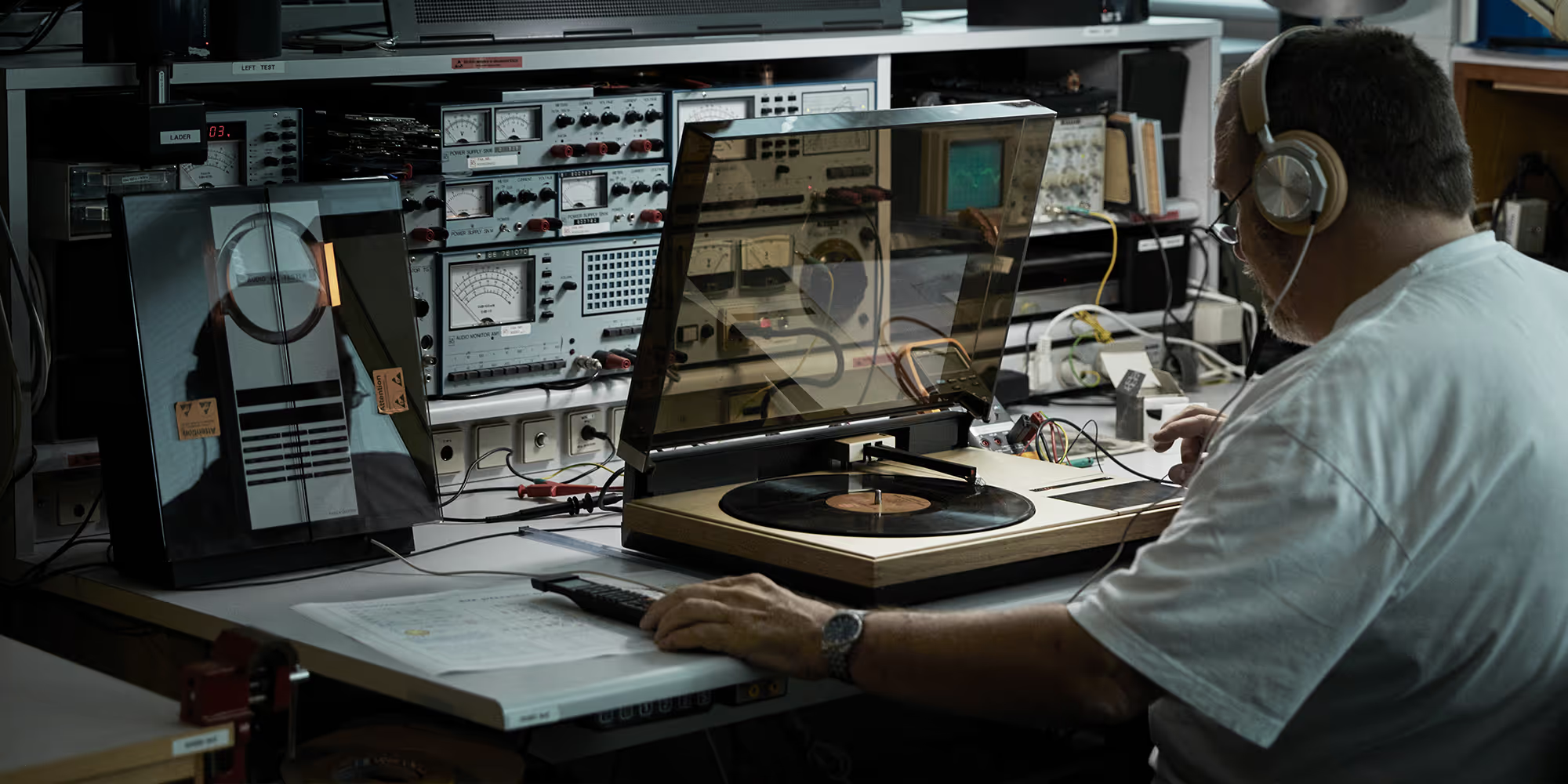
Inside Bang & Olufsen’s laboratory: reimagining the Beogram 4000 turntable
Behind-the-scenes of the iconic record player’s resurrection.
When Bang & Olufsen began creating what would become the iconic Beogram 4000 series turntable, its inspiration was, seemingly, simple:
“The objective was to devise the best and easiest way to play a record, rather than to design a new record player,” shared B&O in its catalogue for the Beogram 4002 model.
“‘Best’ in terms of technical finesse. And ‘easiest’ in terms of operation…. The sound reproduced is as close to the original as modern technology permits.”
Debuting in 1975, its Beogram 4002 record player was the realisation of the company’s ‘form follows function’ mantra in technologically-driven, design glory.
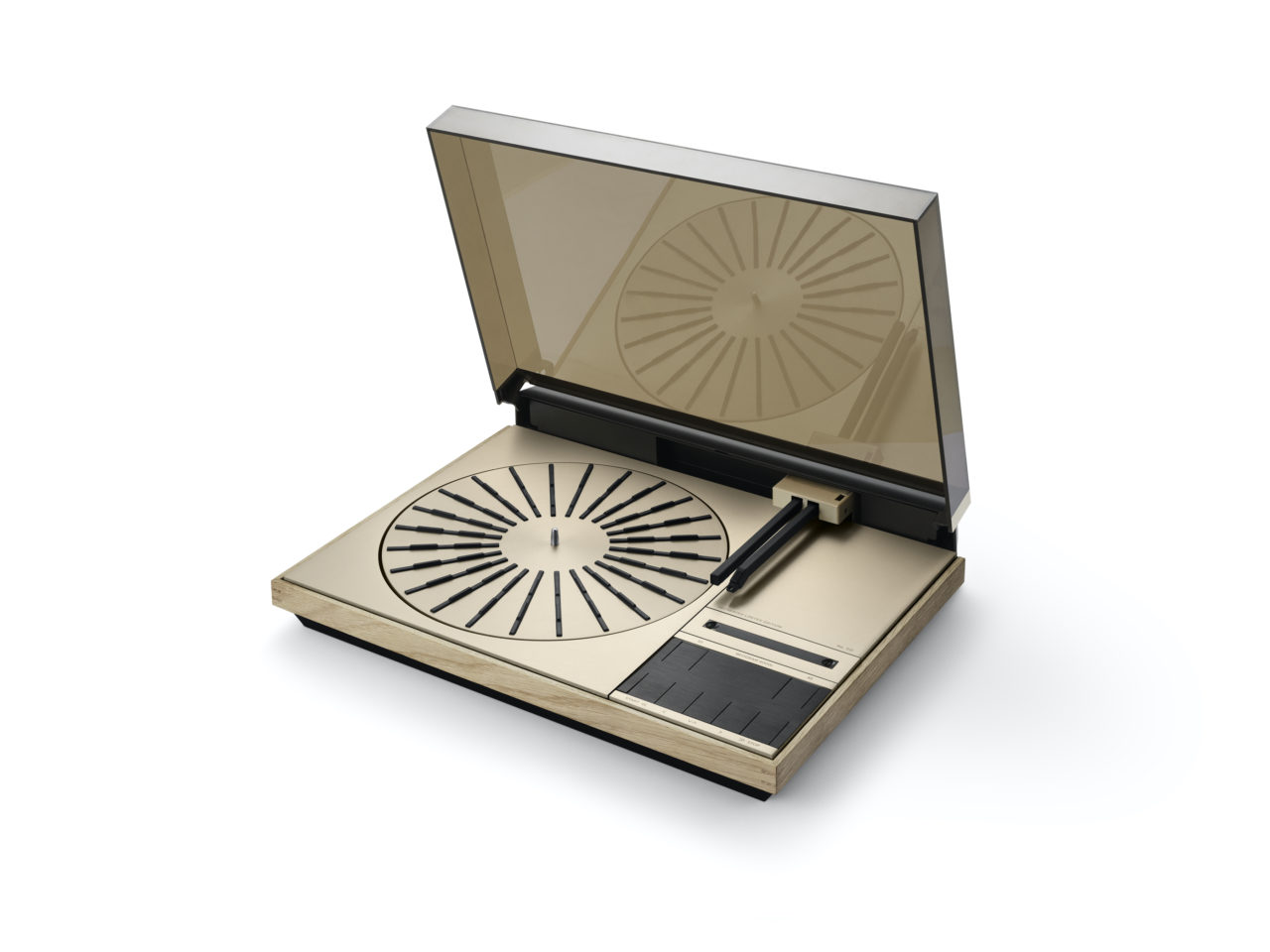
The turntable is accurately self-described as: “a no-compromise, electronic gramophone featuring absolutely top specifications and obsolescence-proof design” – a statement that holds true decades later. The 4002 was the first turntable model to feature B&O’s signature, automated tangential tonearm, for example.
Coupled with its golden metal exterior, a hypnotic, spirograph-like platter bearing geometric lines, and its atmospheric, smoked cover, the turntable’s external aesthetics are as enticing as the electrical finesse that lies within.
Ninety-five years after B&O’s inception, the company launched the Classics Program – dedicated to reimagining its most beloved products. First up in this series, the iconic Beogram 4000.
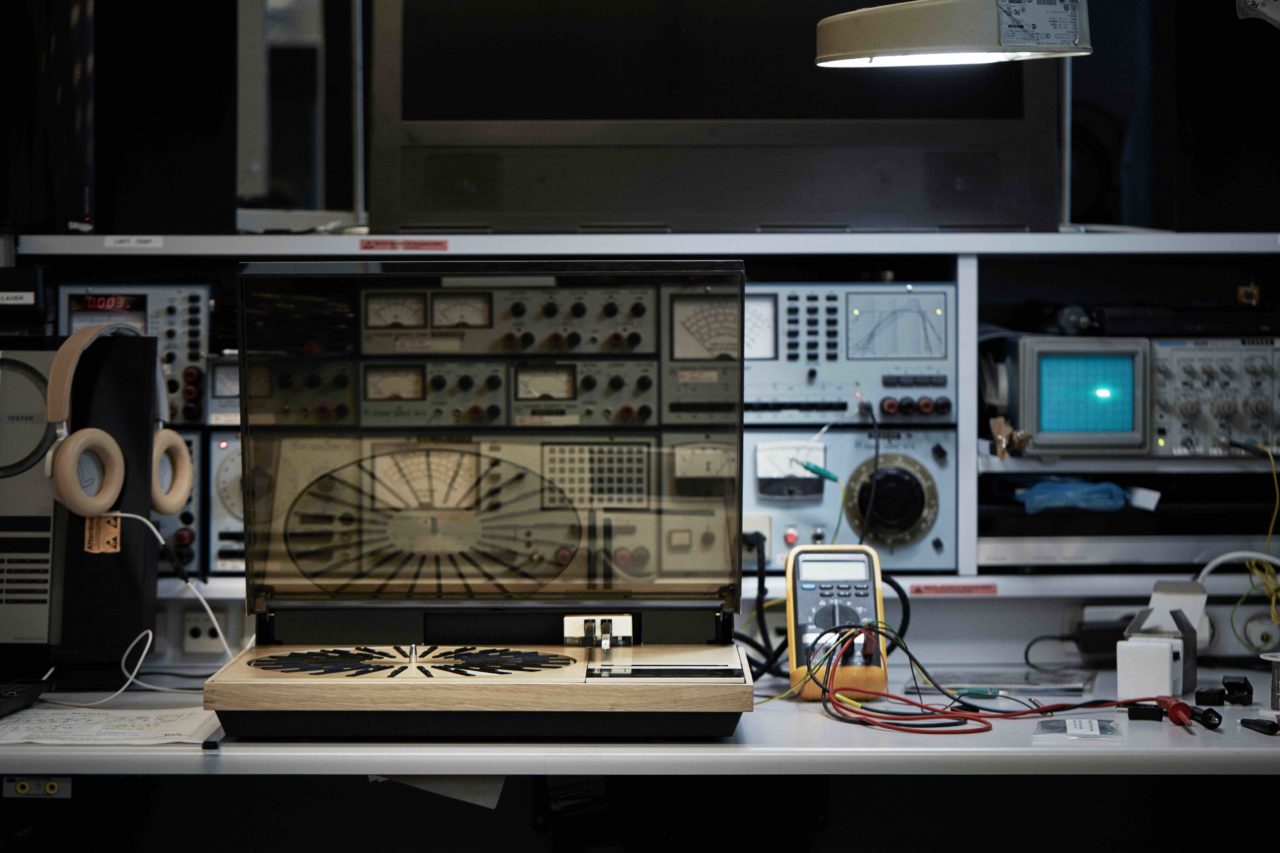
We spoke with Bang & Olufsen’s Senior Global Product Manager Mads Kogsgaard Hansen to find out more:
Why did B&O choose to recreate the 4000c for this series?
It was not a difficult task to choose the first product to be recreated as part of our Classics Program. First of all, Bang & Olufsen has a strong history with turntable design dating back to the 1960s. Furthermore, vinyl still represents a relevant music format, which can offer something different than on-demand streaming services and curated playlists, it allows for a very physical music experience, which perfectly sets the scene for what Bang & Olufsen’s Classics Program stands for – long-lasting and immersive music experiences.
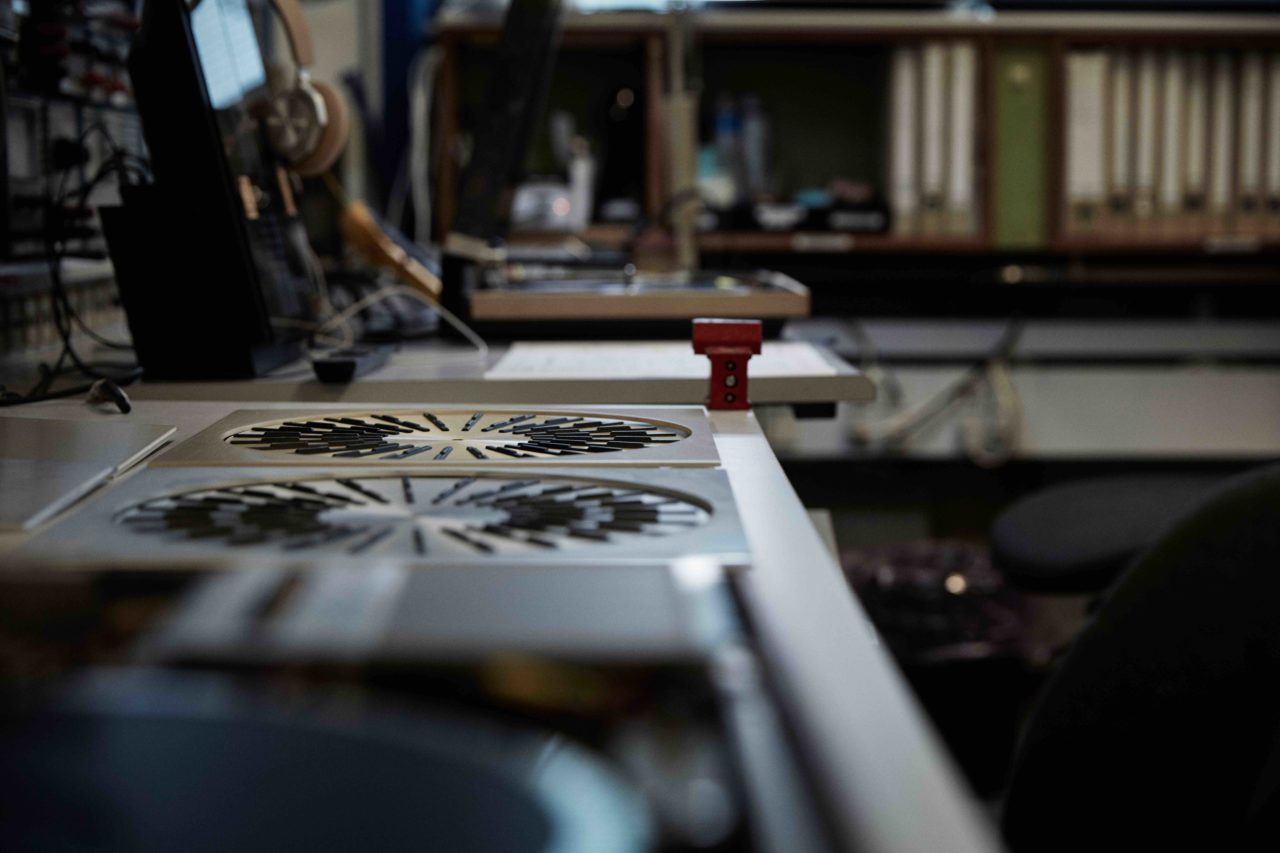
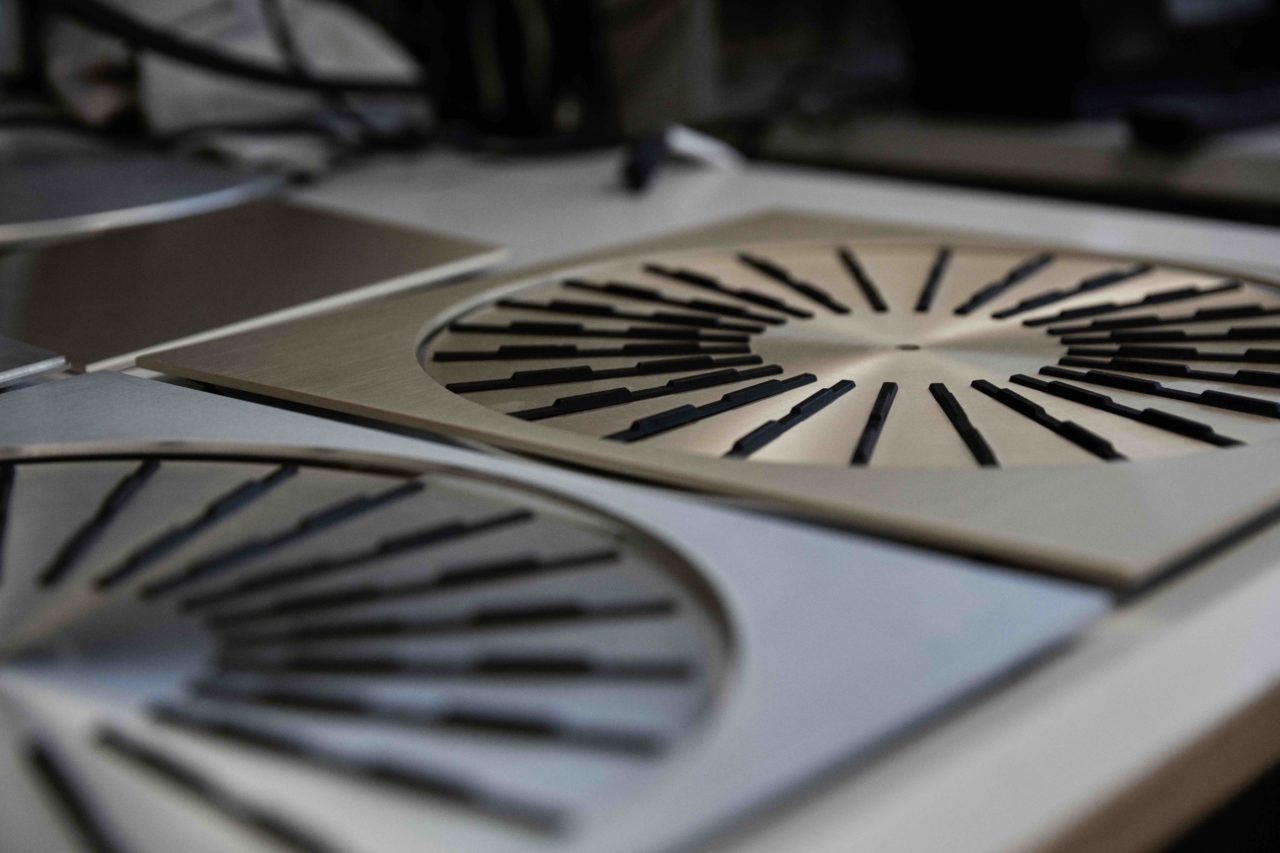
Bang & Olufsen has created many interesting turntable designs through the decades but the Beogram 4000 Series of turntables stand out as something truly special. It came to life with the launch of Beogram 4000 in 1972 and later evolved into the Beogram 4002/6000/4004 models. The Beogram 4000 was the first turntable series with integrated and fully automated tangential tonearm design, which in many ways represented progressive design and breakthrough innovation in Bang & Olufsen history. The Series was designed by Danish designer Jacob Jensen and has for over almost five decades, been recognized as one of the finest turntables ever made. To this day, it is still part of the permanent Architecture and Design exhibition at MoMA in New York.
B&O’s classics initiative “brings pre-owned, original models back to the factory where they were originally created” – what’s the significance of this from a technical perspective?
The fact that the pre-owned Beogram 4000 Series turntables were returned to the same factory facilities where they were originally created has been of key importance. Not only because this journey represents a full circle of the product life, but also because some of the same hands and competencies involved in the original creation and build were working on the classics program. Making a 40-year-old turntable look and perform like new is not an easy task and requires deep knowledge and unique skills alongside the very manual and careful handcrafted process of restoration and assembly.
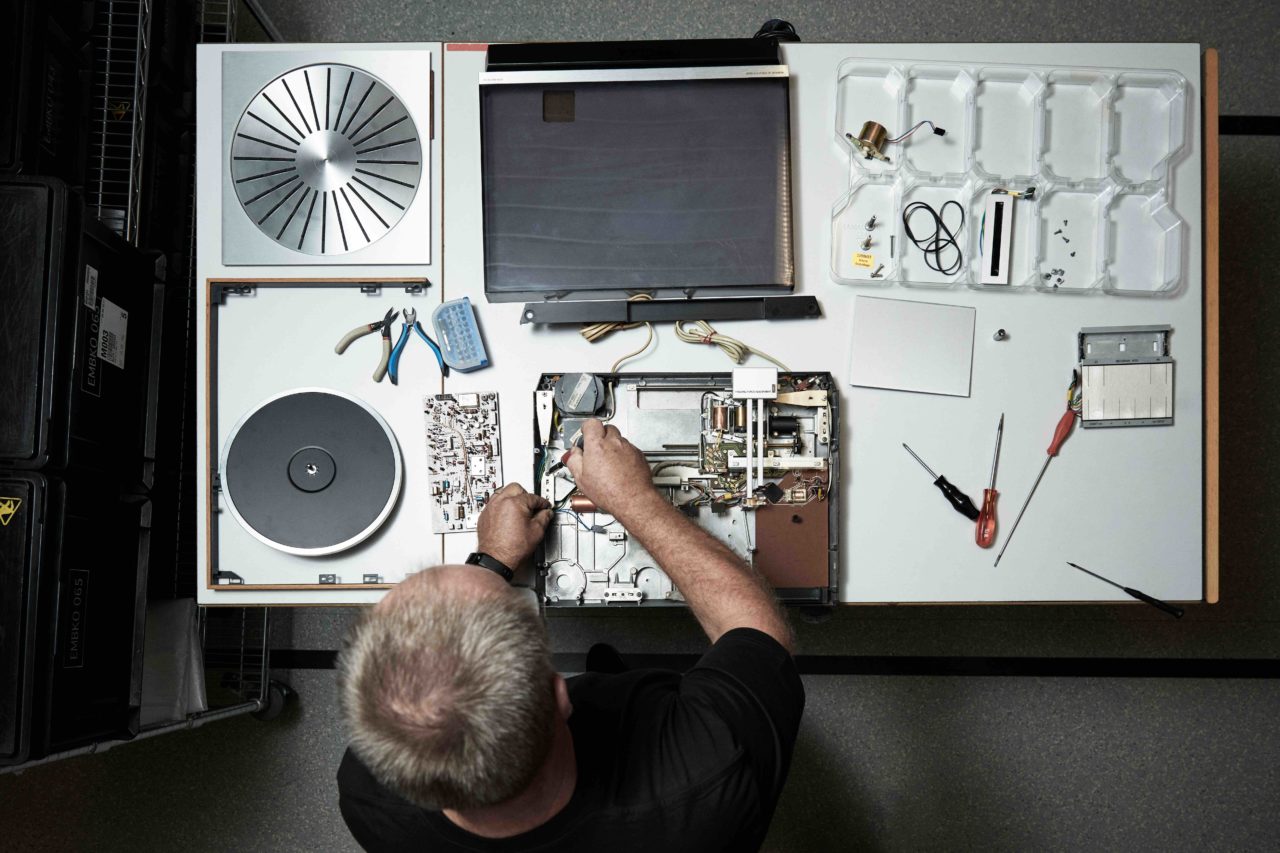
Did this make the redesign and reengineering process easier?
It is fair to say that the recreation process would not have been possible without the involvement of some of our very experienced technicians from the Service Laboratory in Struer, Denmark. As part of the development process, we have also had the chance to involve former Bang & Olufsen employees working with the brand in the 1970’s for their advice and historical knowledge. It has been a fantastic way of working and has certainly created even stronger ties and relationships between our past and our present.
What was the collaborative process between the engineering team and the design team like?
When a Bang & Olufsen product is created, it is always based on a collaborative approach. This has also been the case for the development of the Beogram 4000c. Being a designer at Bang & Olufsen is never just about aesthetics, it is about creating the best possible experiences to our dedicated customers.
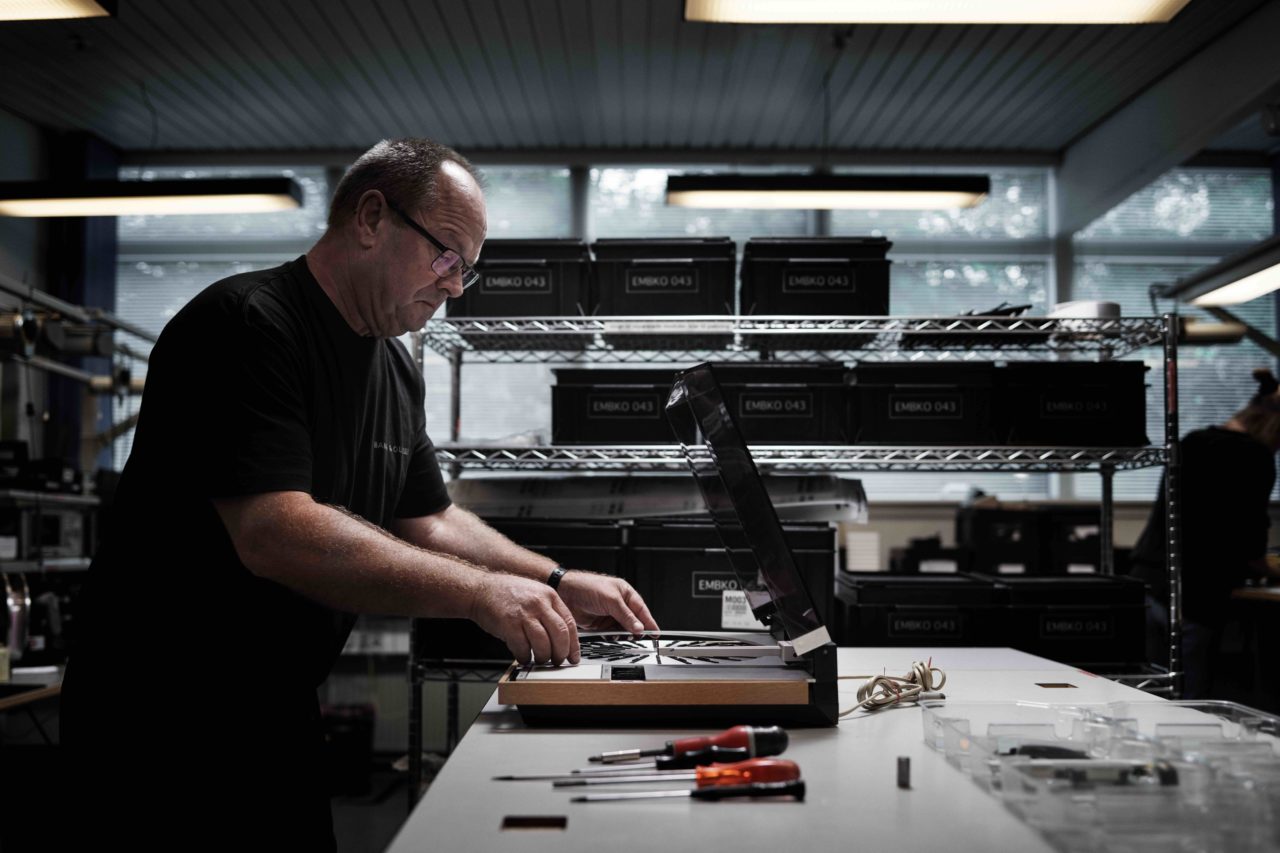
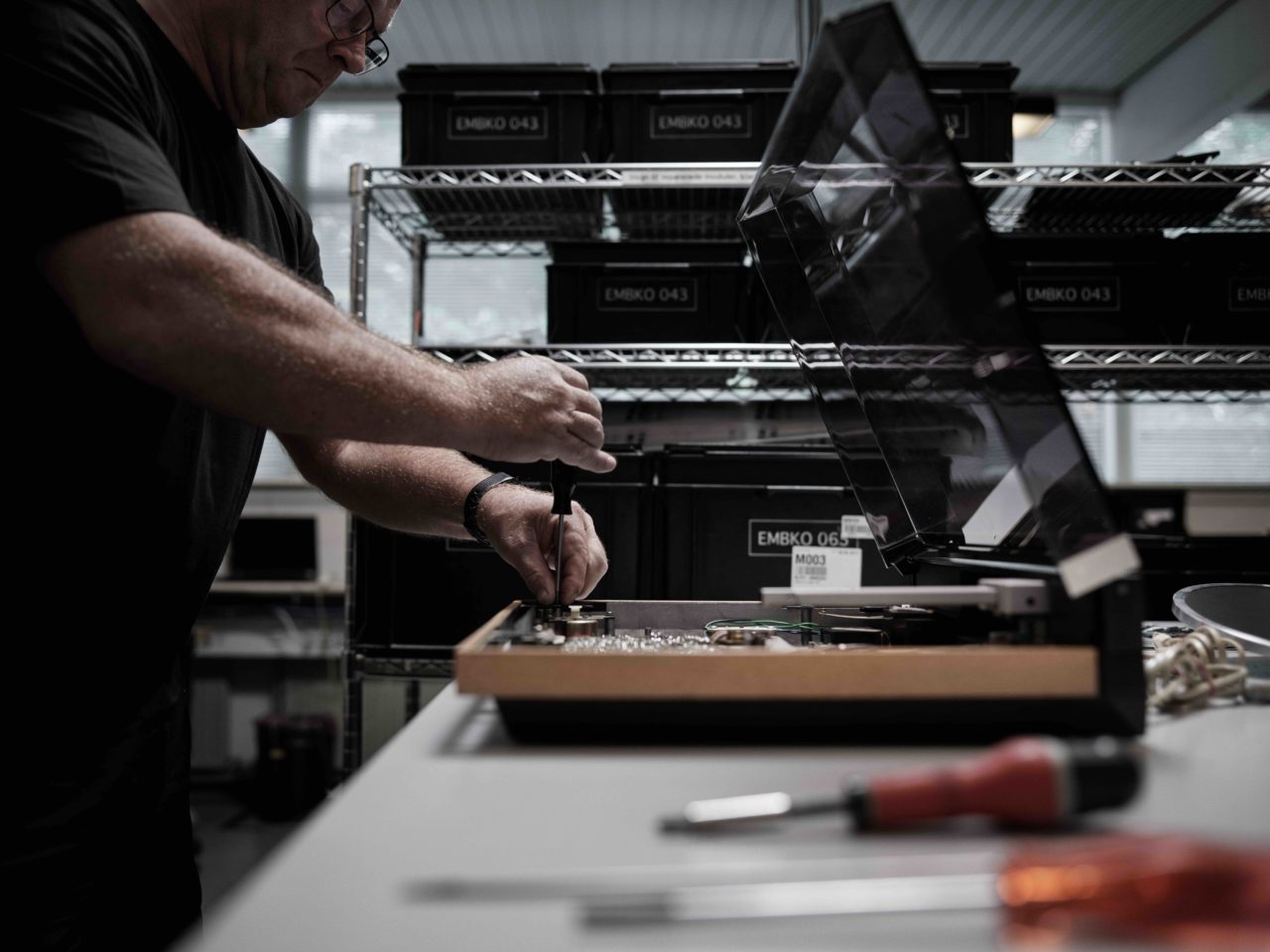
The original design process for Beogram 4000 was also very much a collaborative process with the right level of constructive tension to create only the best. The design was the result of the ambition to create the perfect turntable and reproduce music in the same way as it was cut on the record. Out of this came the dual tonearm tangential tracking design, which very much came to life from our ethos that ‘form must follow function’ in collaboration between the design and engineering team.
How long did the redesign process take?
The concept for recreating the Beogram 4000 Series turntable was born out of the challenge of reimagining the turntable and how it would look and integrate into our product portfolio today. It quickly became clear that the timeless qualities and modularity demonstrated by the Beogram 4000 Series design made it very intuitive and meaningful to bring the look, feel and functional properties to a state of perfection for our contemporary portfolio of audio products.
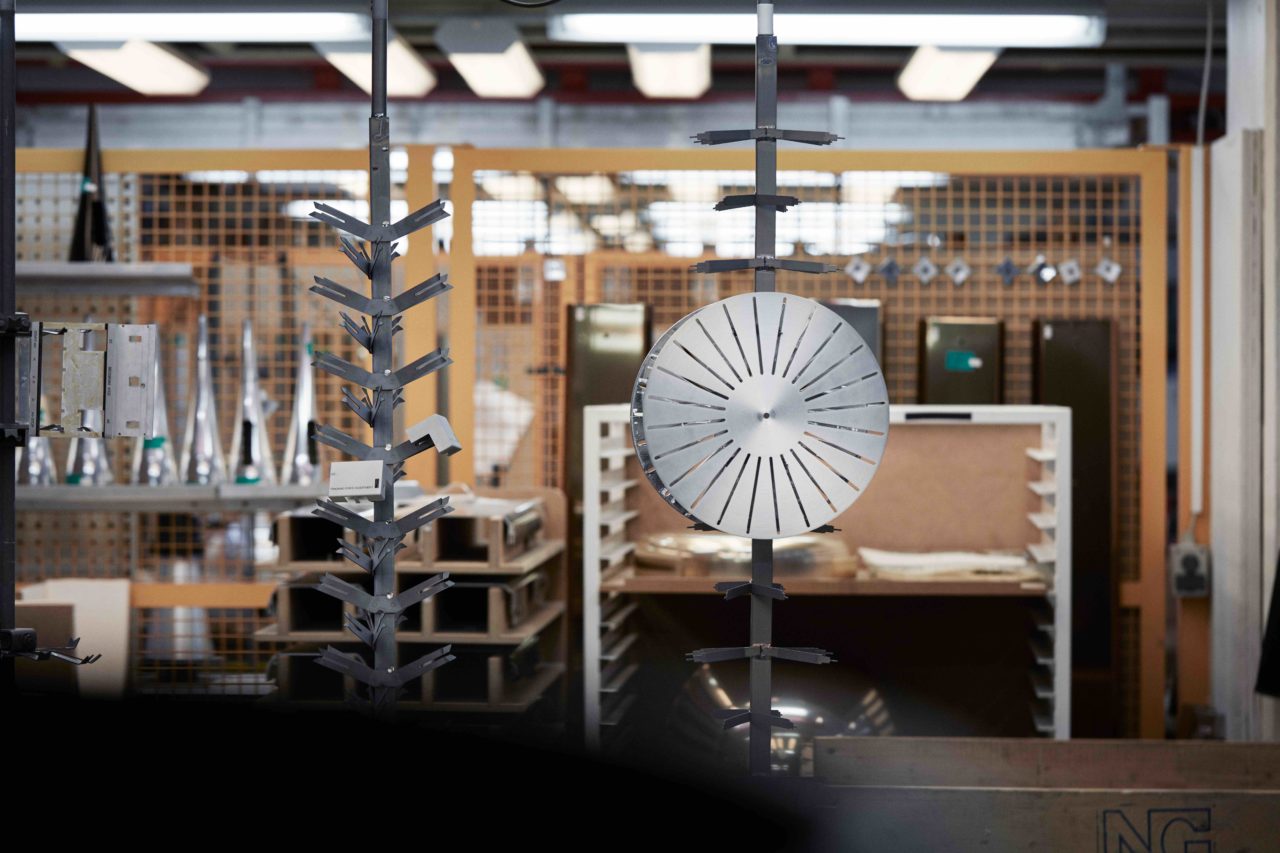
How long did it take to build a single 4000c unit, and who was involved?
The process of recreating the turntables is far from an automated mass production set-up. It is a restoration, and recreation process, which is made individually by hand and very much an exercise of careful craftsmanship and patience. It takes hours to make a unit and bring the level of details and quality we require for a product like this.
The process starts with bringing home the old turntables to the same facilities as they were created. Every unit is disassembled manually, and inspected carefully, before being refurbished and restored to full functionality. Then the re-creation work starts with the purpose of adding beautiful new design elements to the original, to make it look and feel truly unique and prepared to last for decades to come. The final step is to add some technology upgrades to prepare for integration with modern speaker technology and future-proof sound reproduction. Everything is crafted and built by hand by our skilled technicians at the Classics laboratory and aluminium manufacturing facilities in Struer.
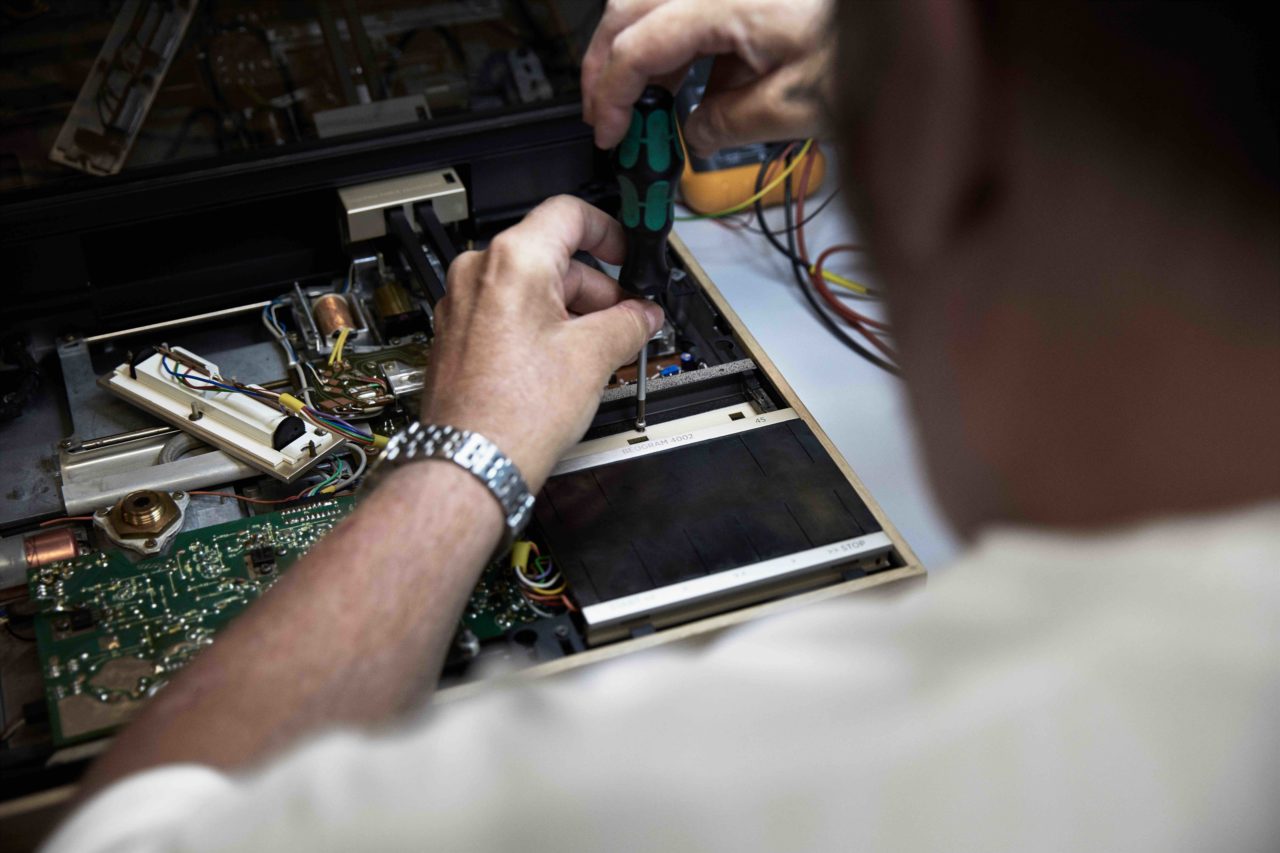
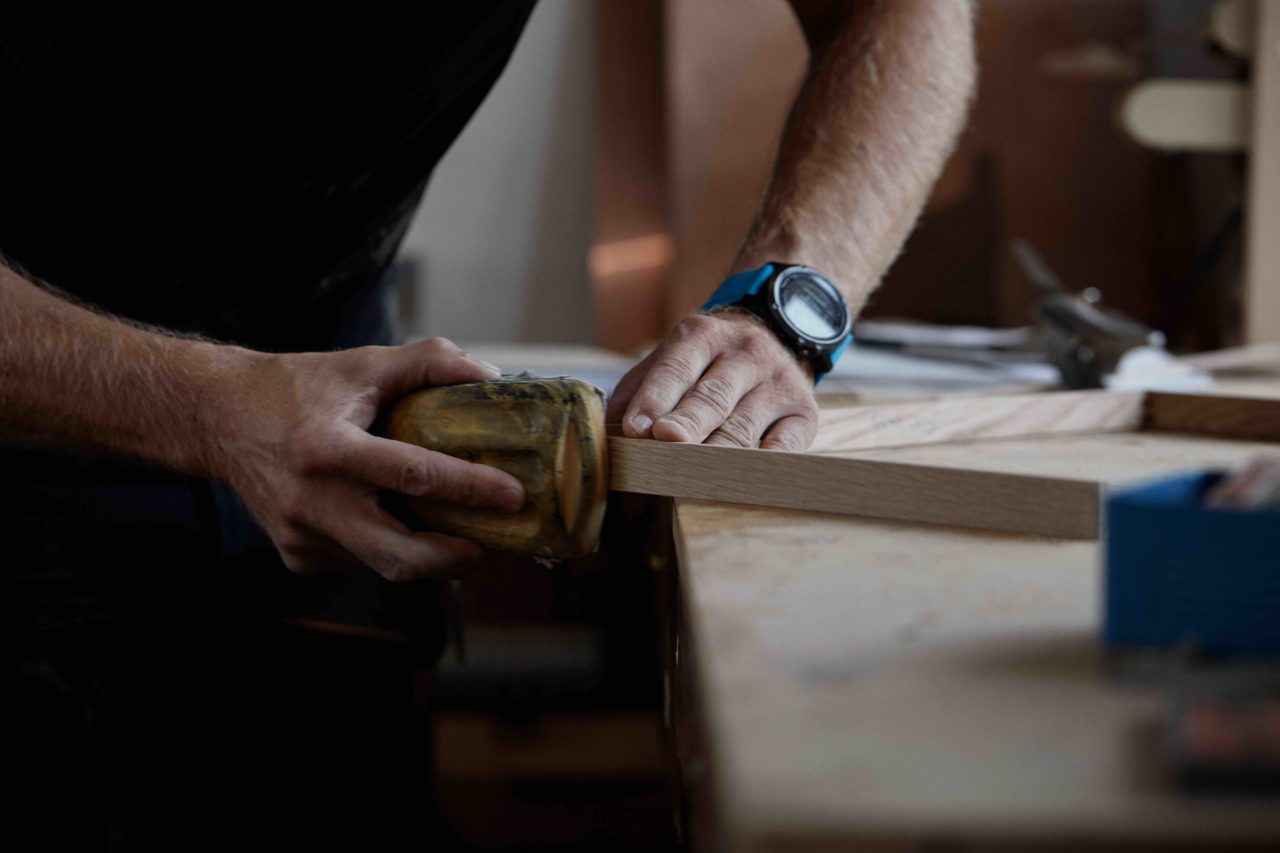
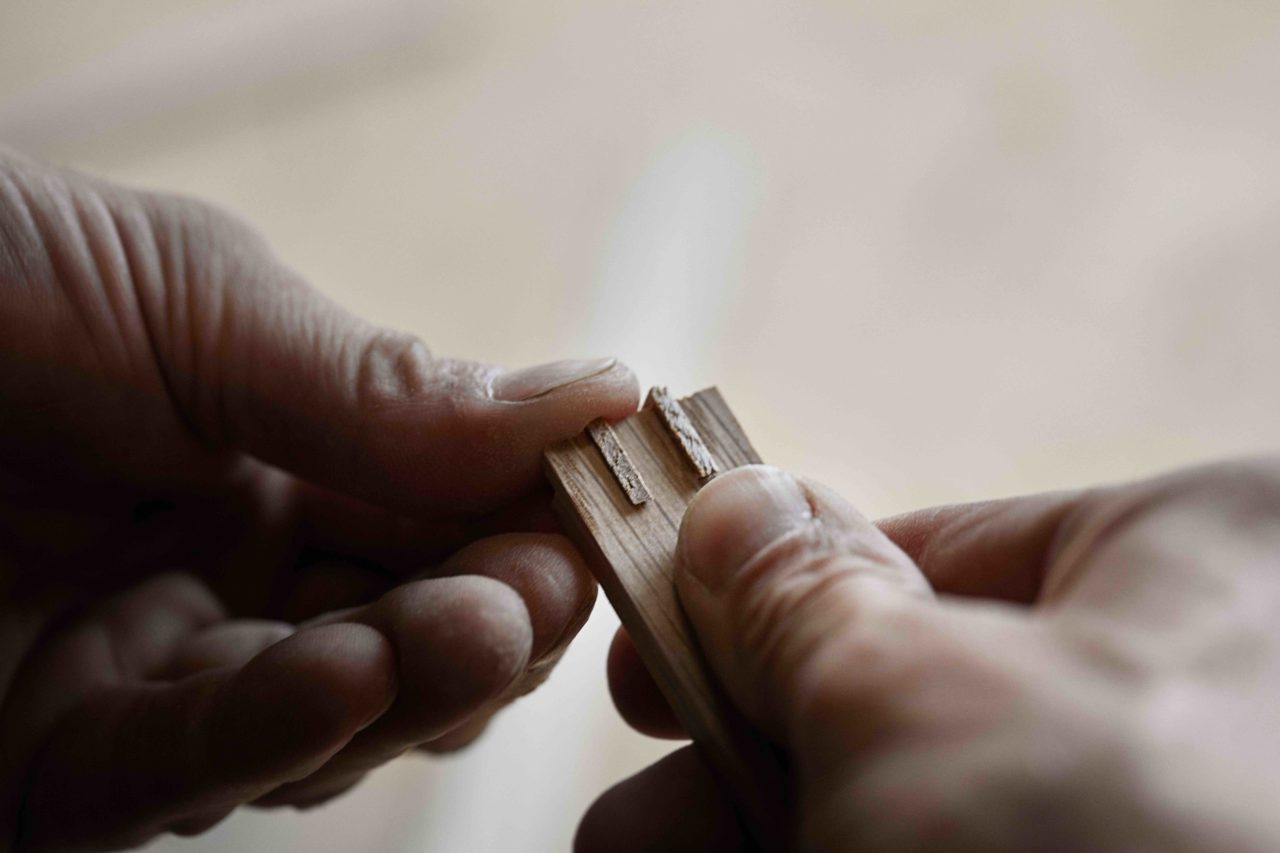
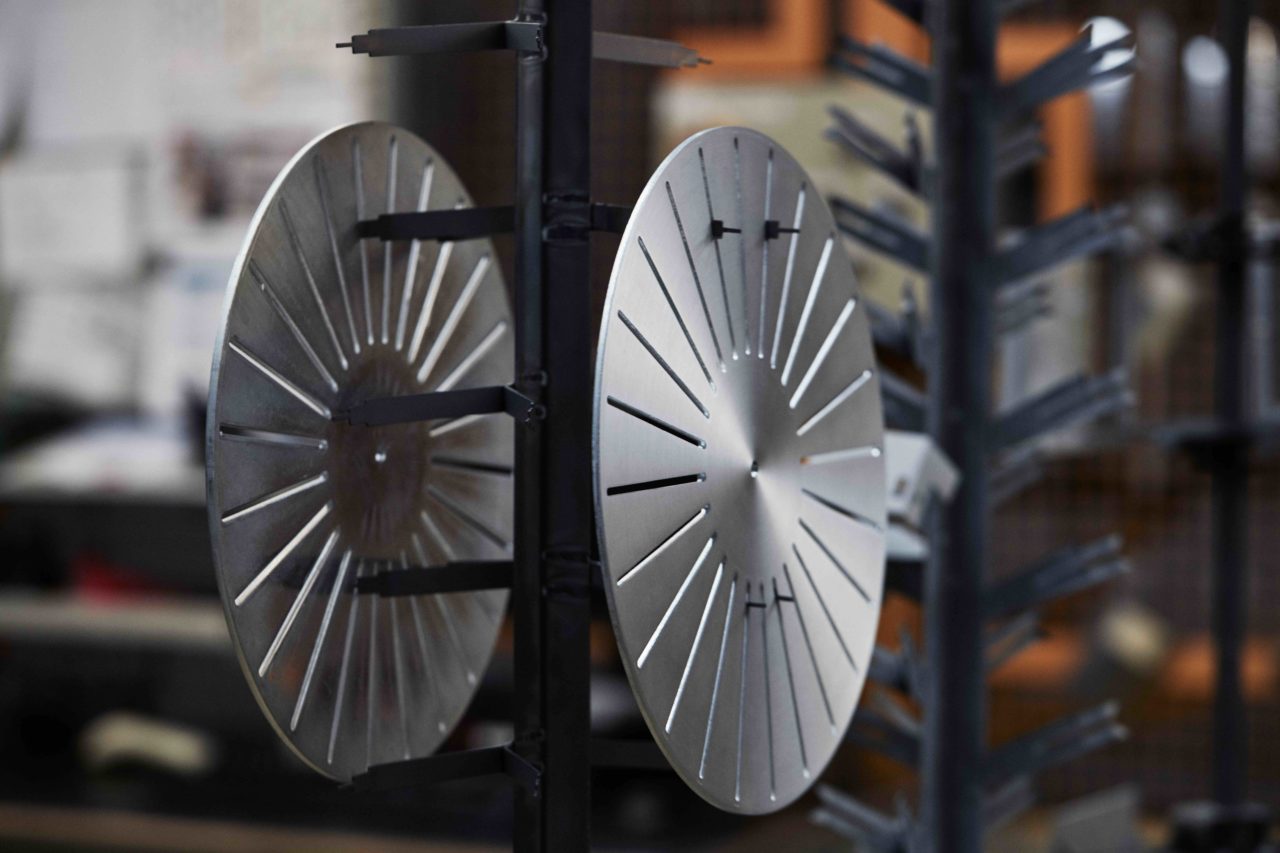
How big was the team that worked on its redesign?
The team working on the Beogram 4000c redesign has been a broad one because of the complexity and many disciplines involved in making something special like this possible. There has been involvement from our engineering team, design, acoustics, procurement, quality, service, marketing, and product management, and even with former and now retired Bang & Olufsen employees. In that sense, the project has been truly multidisciplinary, but also something which has created a lot of good relationships, passion and pride in our organisation, which celebrated its 95th anniversary in November 2020. The team members have each played important roles within their areas of expertise throughout the process – from briefing, concept creation, engineering & development, prototyping, acoustic performance validation, sourcing, ramp-up fulfillment, go-to-market planning, and launch campaign creation.
What challenges did you face in the process?
As no one has really done something like this before, there have been some challenges in the project. Developing the right concept for the Beograms to enter their second life in style was a creative challenge we undertook with fair amounts of humbleness. It has been very important for us to reimagine the turntable, but in a way where the original design intent was respected in the proper way. We believe we have succeeded with this. Then of course there has been technical challenges in finding and creating the needed components for a full electrical and mechanical restoration. The biggest challenge of all has been to develop a robust system for the recreation process based on individualised restoration plans, respecting the fact the each of the 95 units have had their own individual life story and reflect the state and condition of this. Taking 95 different starting points, and bringing them all to the same level of execution and quality has not been easy, but we now have a robust process in place to solve this.
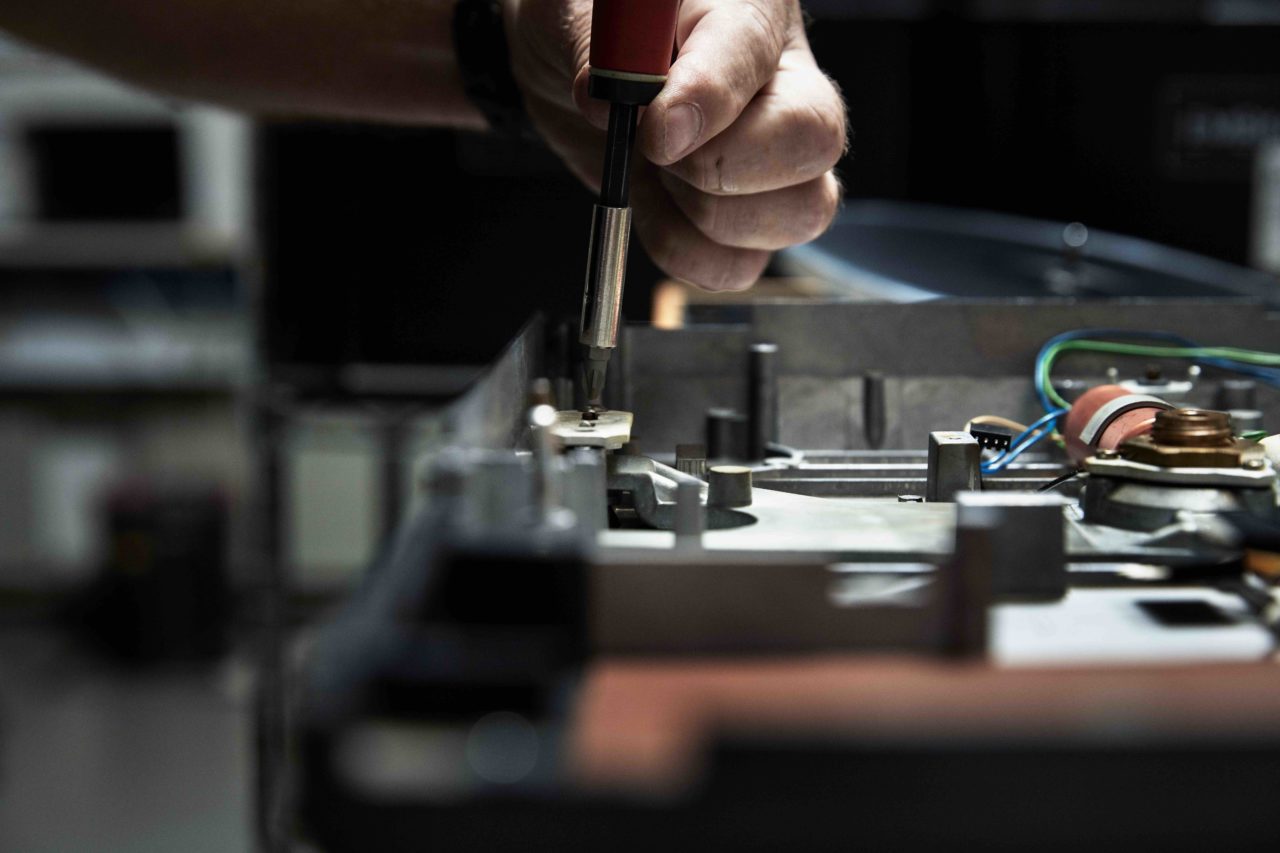
How did you decide what parts of the turntable you’d update/and what would remain the same?
It has been the clear ambition to keep as many of the original components and materials as possible. But is has also been important to focus on making the turntables look new and contemporary and find ways to integrate the past with modern speaker technology to show a case for longevity and relevance through decades. To make the recreated product look desirable, the visual surfaces have been refreshed and the original aluminium parts have been re-machined in our aluminium factory in Struer. For the technology parts we have added a new pickup cartridge based on original Bang & Olufsen specification to future-proof the turntable for further decades and we have also added a build-in RIAA pre-amplified to enable wired connectivity to modern speaker products. An upgrade feature, which was originally designed into the product in the 1970’s as an obsolescence-proof feature, which we are now taking advantage of. The new design elements, which have been added include a new dust lid, the crafted solid oak panel and new fabric signal and power cables as nice aesthetic details.

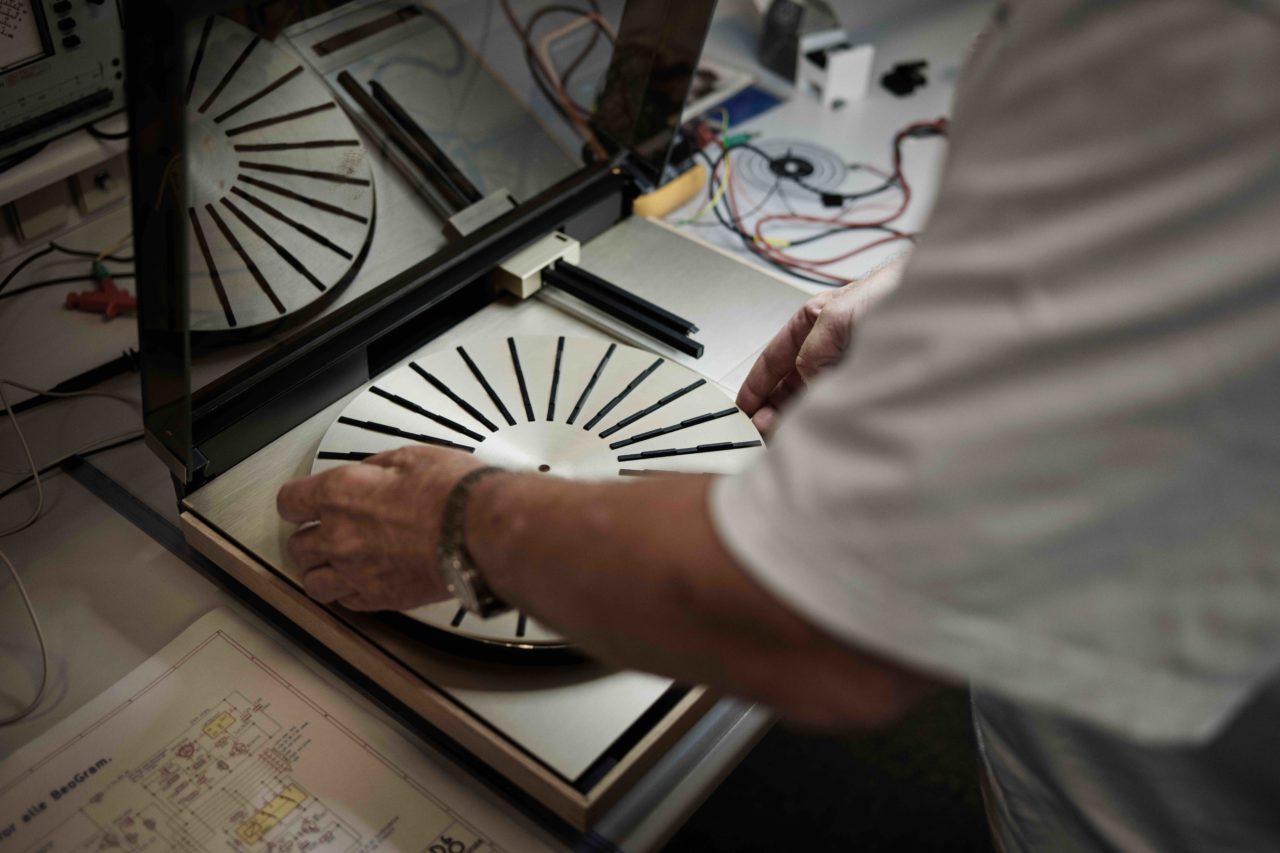
What’s next?
The creation and launch of Beogram 4000c Recreated Limited Edition started out as a pilot project to explore solutions to preserve the heritage of classic Bang & Olufsen designs and with the ambition of showing progressive ways of keeping timeless design relevant and demonstrate longevity of audio products through decades. The pilot project will now evolve further to the Bang & Olufsen Classics Program and we will continue the journey of re-creating timeless classics, exploring circular solutions, and unfolding the cultural impact of music for future generations to enjoy and appreciate.
All photos courtesy of Bang & Olufsen.